A racecar on a track can stop one of two ways. If the driver applies the brakes, the reduction in speed is controlled and gradual. If the car hits the wall, the change in speed is abrupt and violent. The car will likely sustain mechanical damage as it absorbs the change in energy.
In applications involving high inertia load, a sudden stop at the end of stroke can cause mechanical shock, with effects ranging from a mild annoyance to serious operator risk and equipment damage.
End-of-Stroke Shock Damages Equipment and Creates a Safety Risk
When the load moved by a cylinder comes to a sudden stop, it applies stress to the cylinder and the machine’s mechanical structure. Excessive stress on structural components and pressure spikes in hydraulic tubes or hoses can cause premature cylinder failure. Shock also degrades machine productivity by jolting material out of a bucket or container.
Another, even more critical concern is operator safety. Hard stops can throw equipment operators off aerial platforms, or they can be struck by falling debris. Position-sensing cylinder technology is one way to prevent end-of-stroke shock, but it can be expensive. A more economical option for mobile equipment OEMs is adding cylinder cushioning to your design.
Cylinder Cushioning Options for High Speeds and Heavy Loads
Hydraulic cylinder cushioning slows the speed of a cylinder piston before it reaches the end caps. Decelerating the cylinder rod near end-of-stroke stops the piston from striking the hydraulic cylinder ends, preventing mechanical shock. Additional benefits include:
- Reduced noise and vibration
- Improved performance when moving heavy loads at high speeds
- Less cylinder maintenance and an extended operating life
Cylinder cushioning for hydraulic cylinder ends comes in two options: spear-type cushioning and piston cushioning. We’ll go into detail on the technical differences below.
Spear-type Cushioning for Hydraulic Cylinder Ends
Spear-type cylinder cushioning is common in tie rod construction cylinders but is also utilized on welded construction cylinders. You can find both adjustable non-adjustable spear-type cushioning for heavy loads. This type of cylinder cushioning can be effective but has some shortcomings to consider.
The design has a spear or sleeve that enters and exits a concentric pocket. If the spear and pocket diameter difference is too small, there is a risk of metal-to-metal contact and galling. If the clearance is too large, the effective orifice will be too large, making the cushion ineffective.
A downside from the design standpoint is that the cushioned flow has two parallel paths. Oil flows through the annular area created by the spear and pocket and across the fixed orifice or adjustable needle valve, resulting in a complex scenario for predicting the flow. The spear-type cylinder cushioning design requires space in the head and end cap for the cushion adjusting needle valve and the check valve for incoming flow.
Lastly, although the ability to adjust the cushion may have advantages in some circumstances, it also allows for incorrect adjustment. For example, an operator seeking to improve productivity without understanding the potential negative consequences.
Piston Cushioning for Hydraulic Cylinder Ends
Piston cushioning offers advantages over spear-type cushioning for hydraulic cylinder ends. This solution can be designed for a wide range of flows and is more effective in a lower flow range. The controlled flow passes through a single orifice, allowing for more predictable cushion performance. The orifice and the check valve function are built into the piston, keeping the cylinder compact. Piston cushioning is non-adjustable, preventing malfunctions caused by improper adjustments.
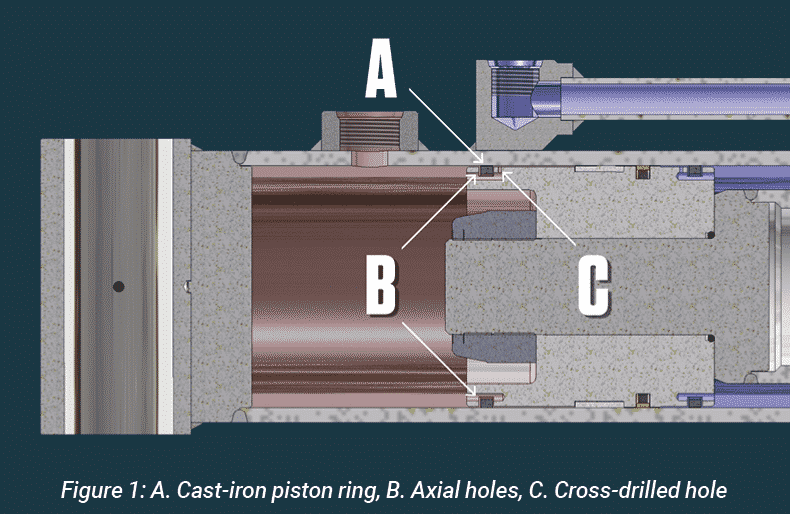
In addition to the typical bidirectional elastomeric piston seal, a cast-iron piston ring is added either on the blind end for a cushion at full retract, on the rod end for a cushion at full extend, or both as shown in figure 1. The groove for the cast-iron piston ring is wider than normal, allowing it to shift slightly in the groove. In addition, there is a series of axial holes and a single cross-drilled hole on each end of the piston.
These features do not affect the cylinder operation during most of the stroke. Flow can freely enter and exit the cylinder, and the elastomeric piston seal prevents internal leakage. The cast-iron ring can “float” in the wide groove, and the pressure is the same on both sides of the ring. When the cast-iron ring passes the port, the exiting flow is forced through the axial and cross-drilled holes, creating a pressure drop. With higher pressure on one side, the ring is forced to the opposite side of the groove, and flow must pass through the single cross-drilled hole.
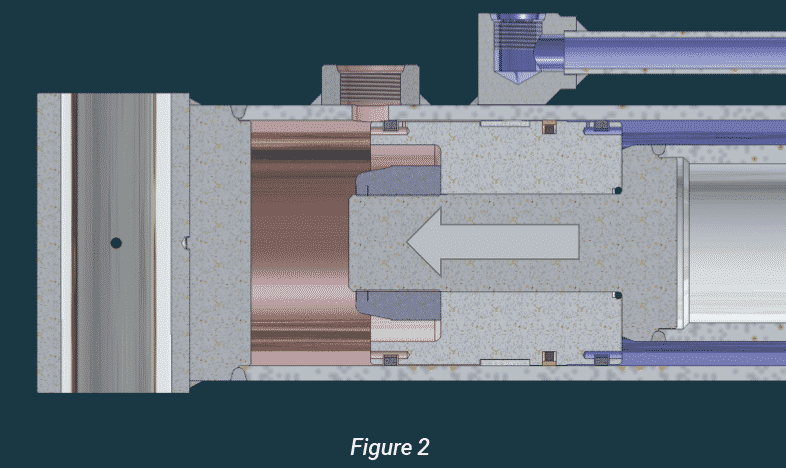
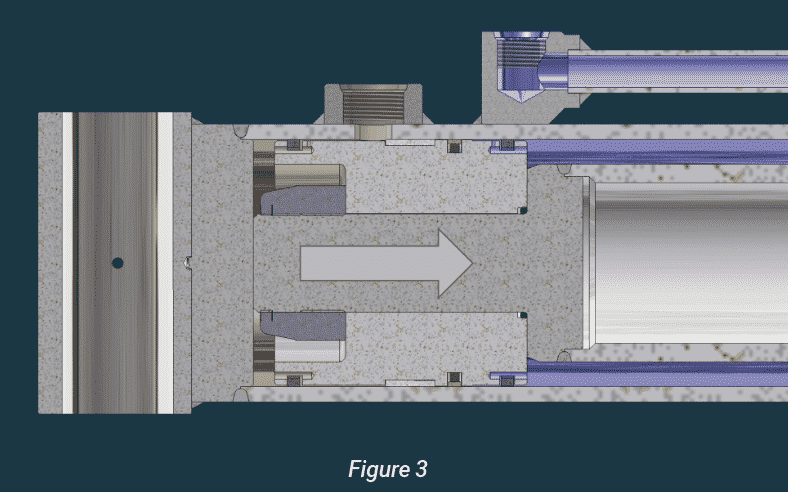
The Effects of Pressure on Cylinder Cushioning
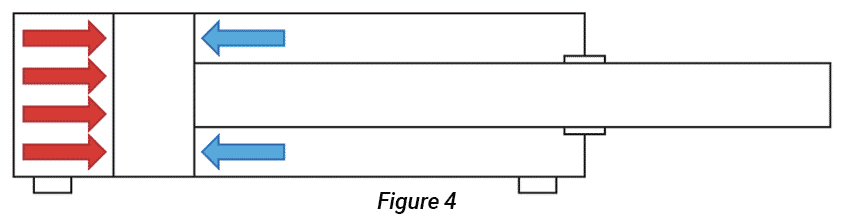
When working with cylinders with any cushion, it is vital to consider the possibility of pressure intensification. To reduce the cylinder speed, the exiting flow must be restricted so that the incoming flow reaches the maximum pressure. However, because of the area difference on each piston side, the exiting flow will not be the same pressure as the incoming flow.
On the extend-side, also known as the blind or cap end, the fluid under pressure acts on the full bore diameter of the cylinder. On the retract- or rod-side, the fluid under pressure does not act on the center area because of the rod; it only acts on the annular area between the rod and bore. The ratio of the extend-area to the retract area is known as the cylinder ratio. The cylinder ratio is typically in the range of 2:1 to 3:1, but if the rod is large relative to the bore, it can be as high as 10:1 (figure 4).
If the pressure is controlled by a main system relief set at 3,000 psi (207 bar) and the cylinder has a ratio of 2:1, when the cylinder is retracting and the cushion is active, the rod side pressure increases to 3,000 psi (207 bar). Because the extend side area is greater by a factor of two, the resulting pressure on the extend side is calculated by dividing by two, or 1,500 psi (103 bar).
This pressure is used to design the control orifice size in the piston for the designed flow rate. If the same cylinder has a cushion at full extend and the extend side pressure increases to 3,000 psi (207 bar), the resulting pressure on the rod side is 6,000 psi (414 bar). This higher pressure is completely contained within the cylinder and is not measured with a cylinder port gauge, nor can it be prevented or limited with the addition of an external relief valve.
In addition to using this pressure to determine the orifice diameter, this higher pressure must also be considered when selecting seals, tube wall thickness, and head retention methods to prevent cylinder failure. If the cylinder has a relatively large diameter rod and therefore a high cylinder ratio, it may not be economically feasible to design the cylinder for the resulting rod side pressure even at low system pressures.
It may be necessary to add a relief valve set at a lower pressure specifically for the extend-side of the cylinder. If that will not provide adequate extend-force, the cylinder may not be a good candidate for a cushion at full extend and deceleration should be accomplished by a different method.
Although removing the potential for incorrect adjustment may be a benefit in some applications, in others the benefits of adjustment outweigh the risk. It is possible to adapt the cushion piston design to accommodate an adjustment valve in the end cap or head gland for these applications.
Maintaining Cylinder Cushioning and Protecting Your Equipment
As with all hydraulic components, the introduction of a control orifice makes it more sensitive to contamination. A small particle can block or restrict flow, negatively affecting cylinder cushion performance. It is important for proper operation and long life to perform regular preventative maintenance and maintain fluid cleanliness via proper filtration.
A welded cylinder with a properly designed cushion piston is analogous to properly applied brakes. As the energy is transferred to hydraulic heat and the cylinder stops in a controlled manner. This can provide a significant benefit to the machine and the user.